Unlock content
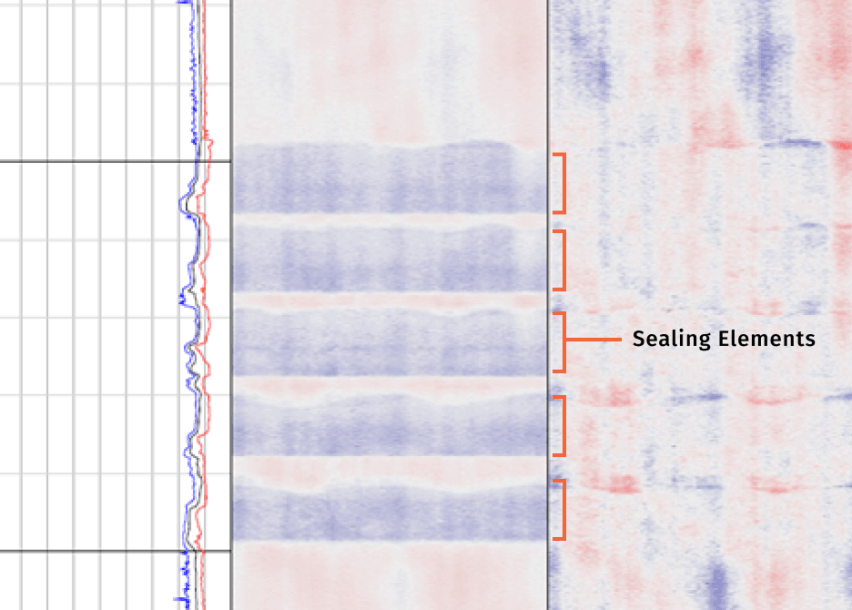
Share this
An established offshore operator faced challenges with a Downhole Safety Valve (DHSV) assembly in a production well. The operator suspected possible scale buildup, an incorrect position of the flow tube element, or mechanical damage to the valve body from previous operations. In an effort to temporarily address the problem, a straddle was set across the DHSV assembly but failed, resulting in lengthy mechanical clean-out runs, additional delays, and downtime.
The operator deployed HADES-R to evaluate the condition of the DHSV:
1. Identify any scale buildup, mechanical damage, or deformation on sealing surfaces and components.
2. Verify the flow tube was positioned correctly.
3. Measure the internal diameter (ID) and pass-through diameter of the bumper sub and pup joint assemblies above and below the valve to ensure the correct straddle or shallow set plug is selected.
Following the rapid deployment of HADES-R, a detailed analysis of the DHSV assembly was prepared for the operator. The analysis yielded clear and definitive results. The downhole safety valve was measured to be clear but not in the correct configuration. Acoustic imaging revealed the flapper valve was fully open and the flow tube was partially engaged. Additionally, the maximum pass-through diameter across the bumper sub and pup joint assemblies was found to have a reduced ID of 113.4mm [4.465in] as opposed to the nominal ID of 115.5mm [4.547in]. Identifying this 2.1mm [0.083in] ID difference was crucial for successfully selecting the correct straddle in subsequent operations.
The insight acquired from the inspection allowed the operator to proceed without delay. The detailed verification of the DHSV assembly’s condition and dimensions enabled the operator to maintain well safety and avoid costly remediation and mechanical clean-out runs across the DHSV.
This case study highlights the value of capturing precise direct measurements of downhole components. Comprehensive assessments are intuitively understood with submillimetric 3D data and are quickly carried out through any fluid clarity.
By proactively assessing potential challenges through detailed examinations, operators are verifying the integrity of critical safety systems and confidently proceeding with operations, minimizing well downtime, and maximizing production.
By clicking Submit you’re confirming that you agree and consent to our Terms and Conditions.