Unlock content
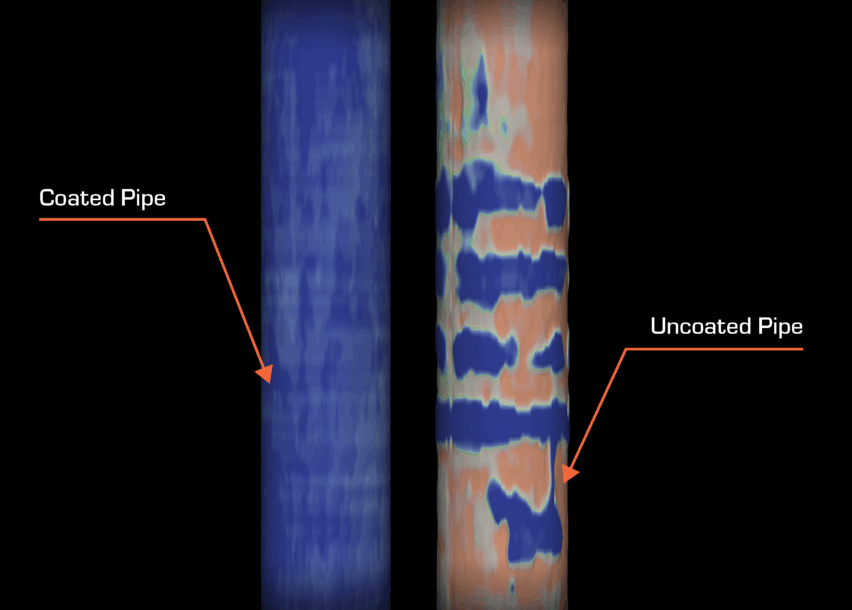
Share this
HADES-R + HADES-T
Objectives
An operator sought to assess the quality of completion of a recently hydraulically stimulated well by evaluating the proppant distribution along the reservoir. Proppant distribution can vary greatly between stages and is often due to stages not being isolated as expected. Plugs not isolating can result in stages being overstimulated while others are under stimulated. These stimulation issues are often undetected at the surface during completions.
The entire well was inspected in a single continuous high-speed pass and all 1198 perforations were evaluated. A comprehensive perforation erosion report informed the operator where the proppant was distributed across the well – on a per stage, per cluster, and per perforation evaluation granularity. Results showed there was a large variation in the stimulation performance between stages of the same design and a detailed look at each plug location was further carried out to understand why.
A multi-view report with acoustic intensity, radial distance, normalized radial distance, and radial wall loss views provided a detailed understanding of each plug location. Multiple stages showed plug slip marks and casing damage at the plug location, indicating a lack of isolation. Stages directly below the plug damage had more proppant entering the stage. Additionally, a plug was identified to have been placed too far downhole, resulting in a stage being stimulated twice.
This detailed plug analysis informed a Root-Cause Analysis (RCA) and resulted in improved plug setting procedures. This led the operator to significantly reduce plug-related issues, optimize subsequent fracturing operations, and prevent over-stimulating stages – avoiding extensive clean-out runs, and costly Fracture Driven Interaction (FDI) impacting neighboring wells. These insights and operational improvements are advantages operators are gaining from DarkVision’s industry-leading high-resolution acoustic inspections.
By clicking Submit you’re confirming that you agree and consent to our Terms and Conditions.