Unlock content
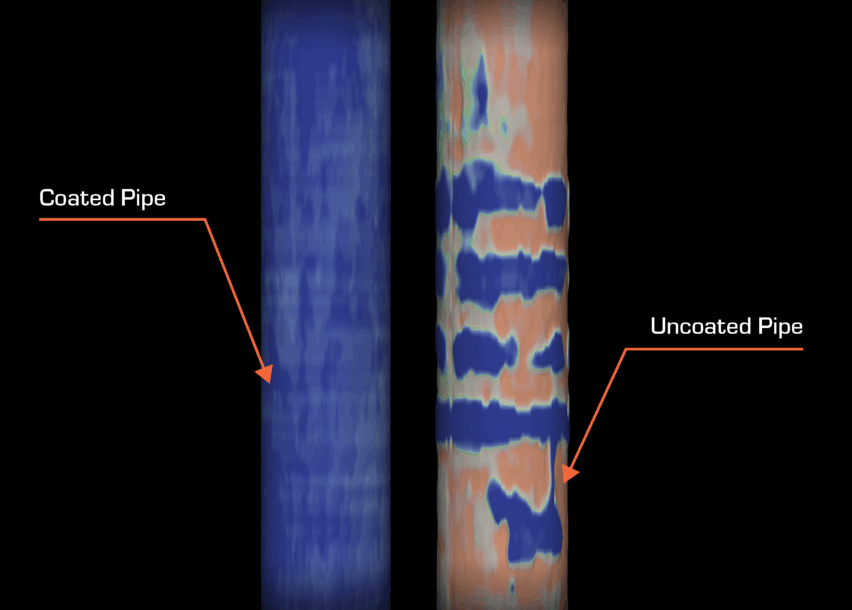
Share this
Haynesville Shale
HADES-R™
An established operator in the Haynesville Shale needed accurate and reliable perforation erosion data to optimize future completion designs across the basin. With a well temperature of 340°F, a robust inspection tool and a service provider with operational expertise working at elevated temperatures was required. These capabilities would ensure the operator received clear, actionable results despite the challenging downhole conditions.
With an industry-leading combination of operational knowhow and the proprietary HADES-R™ downhole evaluation tool, DarkVision scanned the well to a depth of 22,000 ft in a single run. The HADES-R™ high-resolution acoustic imaging system captured submillimetric 3D data of the entire well, identifying and measuring 99.9% of the 1450 perforations. This scan yielded complete and detailed data on cluster efficiency and erosion bias across all stages.
DarkVision also identified plug related casing damage and discrepancies between the expected completion design and the observed placement of perforations and plugs. The submillimetric detail in the volumetric data by HADES-R™ enables DarkVision to identify plug set locations and slippage based on packer and button imprints on the casing ID.
In this well, plugs for multiple stages were observed to have been set downwell from their intended locations resulting in overlapping isolation zones. Perforations in the overlapping areas were stimulated twice, resulting in wasted proppant. One stage was identified with a different cluster pattern and significantly more perforations than was specified in the completion design.
The high-resolution 3D data provided by DarkVision gives operators critical insights into the condition of their wells, and any discrepancies between staging design and final completion, enabling them to make informed decisions on subsequent completion designs. By optimizing cluster designs with guidance from accurate perforation erosion data, operators are seeing up to a 15% increase in production.
By clicking Submit you’re confirming that you agree and consent to our Terms and Conditions.